Understanding and calculating the cycle time is a needful part of making the best of making. Key metrics include machine cycle time, worker cycle time, and working time. The Machine Cycle Time refers to a machine's time to finish and work. Good Machine Cycle Time, on the other hand, only includes the time the machine is working without any breaks.
Worker Cycle Time deals with the time taken by a worker to finish a project. Likewise, Working Time is the length during which a thing is being worked on directly. These metrics give various gains. It helps increase skill, lessen making lead time, and ensures an even order of lead time. It also helps in finding non-value-added time and lessening changeover time.
In turn, this helps in increasing throughput time and the full product cycle time while keeping the Takt time. Overall, understanding and rightly calculating cycle time can lead to making betterments and progress in design.
Introduction to cycle time
Cycle time is a needful part in any making or making process. This refers to the length, also known as Good Machine Cycle Time, needed to finish one round of a work or to make a product go through a certain process, which includes the Machine Cycle Time and the Worker Cycle Time.
In truth, cycle time covers the start from Working Time to Making Lead Time, Throughput Time, and, in the end, the Full Product Cycle Time. The cycle time idea also thinks of Lead time, Changeover Time, and Making Run Time.
Being able to calculate and make the best of these parts can greatly boost skill, leading to good value-added time while making less non-value-added time. Mastering cycle time enables a smoother, more likely Design to Progress Time.
Definition of cycle time
Cycle Time refers to the full time from the start to the end of a process, including working time, non-value-added time and value-added time. It's the full product cycle time from when an order is given until the product is given or the full time taken for one piece to go through a machine or worker. This time includes various factors like machine cycle time, order lead time, making lead time, etc. It's understood as the clock time needed for a product to move all the way through a process or value stream.
Importance of cycle time in production
Cycle time plays a great role in management, especially balancing fruitfulness and skill. For example, the Machine Cycle Time serves as a measure for the skill of a machine in finishing one round of its project. The Worker Cycle Time, on the other hand, measures a worker's fruitfulness rate which affects the overall Product Run Time.
Understanding the details of cycle time parts such as Order Lead Time, Full Product Cycle Time, and Changeover Time can greatly help in finding bottlenecks and needless delays (Non-Value-Added Time). Also, a balanced and good cycle time (Takt Time) can further a steady flow in making stages, in the end leading to making the best of Throughput Time and Making Lead Time.
Understanding the components of cycle time
Cycle time is made of many key parts, including Machine Cycle Time, Worker Cycle Time, and Working Time. Machine Cycle Time refers to the time needed for a machine to work on a certain project or product. Worker Cycle Time, on the other hand, is the time taken by a worker to finish a project or make a thing.
Meanwhile, Working Time is the length needed to change raw goods into finished goods. Understanding these parts helps in the skillful planning and doing of making workings. It helps in making the best of the Good Machine Cycle Time, thereby making the most of making skill and lessening Non-Value-Added Time.
In addition, it plays a great role in finding key making factors such as Making Lead Time, Throughput Time, Order Lead Time, and Full Product Cycle Time. Takt Time and Changeover Time are also greatly affected by these parts.
Start time and end time
The idea of Start Time and End Time is needed in understanding various metrics such as Good Machine Cycle Time, Worker Cycle Time and Full Product Cycle Time. These words mainly calculate the length of a certain process or event within a process. Start Time marks the start of a project or work, whereas End Time shows the endpoint. By rightly measuring Start Time and End Time and comparing it with metrics such as Working Time and Throughput Time, governors can find bottlenecks, unskillfulness, and ways to make the best of making. Also, Start Time and End Time also give needful inputs for finding parts like Making Lead Time and Order Lead Time, which are needful in goods management and meeting customer needs in a timely way
Work in progress (WIP)
In the realm of making and making, understanding certain measurements like Good Machine Cycle Time, Worker Cycle Time, and Making Lead Time can help make the best of the making output. The Good Machine Cycle Time counts for the speed at which a machine can make a part, while the Worker Cycle Time refers to the time a worker takes to finish a round. Making Lead Time, on the other hand, is the full time from when an order is given until it's ready for giving. It covers the Working Time, Order Lead Time, and includes any scheduling buffer time. It's worth noting that unskillful practices within these times are often seen as Non-Value-Added Time.
Throughput
Throughput refers to the rate at which a system makes a product or finishes a process, greatly affecting lead time and full product cycle time. It factors in the good machine cycle time and the worker cycle time, truly showing the system's working time. Making the best of throughput can greatly lessen order lead time and non-value-added time, directly affecting the design to progress time. Adding ways to make less changeover time plays a vital role in making the best of throughput. Thus, reaching a well-set takes time for skillful running time.
How to calculate cycle time
The calculation of cycle time involves determining the time it takes to complete a single unit of a task or process. The Machine Cycle Time is the speed at which a machine completes a task. This can be calculated by dividing the total production run time by the number of units produced.
Meanwhile, the Operator Cycle Time is the time consumed by the operator to perform the task. This also includes any Non-Value-Added Time spent by the operator. It's important to keep in mind elements like changeover time and processing time to ensure effective Machine Cycle Time. Utilizing such measures helps to reduce order lead time, ultimately optimizing total product cycle time.
Step-by-step guide to cycle time calculation
Cycle Time Calculation involves a critical understanding of several different components, specifically Effective Machine Cycle Time, Operator Cycle Time, and Total Product Cycle Time. Initially, Effective Machine Cycle Time refers to the length of time a machine operates effectively on a particular unit, while Operator Cycle Time considers the temporal involvement of any human operators in the process.
These are added together, along with any additional processing time, to calculate the Total Product Cycle Time, the ultimate measure of how long it takes to produce a given unit from start to finish. This calculation allows for a better understanding of production efficiency and areas for potential improvement.
Common mistakes in cycle time calculation
Several common mistakes are often observed in cycle time calculations. First, overlooking the changeover time, which greatly impacts effective machine cycle time, can result in miscalculations. Secondly, not considering non-value-added time can overstate the actual processing time and distort the total product cycle time. Lastly, failing to account for operator cycle time may render an inaccurate representation of production lead time. Care should be taken to avoid these mistakes for accurate and efficient production planning.
Key production metrics related to cycle time
Key production metrics related to cycle time are crucial in monitoring and improving production processes. One of such is the Machine Cycle Time, which measures the total time required for a machine to complete one cycle of operation. It's vital for assessing machines' efficiency and identifying areas for improvement.
Another key metric is the Effective Machine Cycle Time, which considers only the productive time, excluding non-value-added time like equipment breakdowns or setup changes. It provides a more accurate picture of a machine's true productive capacity.
The Operator Cycle Time, on the other hand, measures the time taken by an operator to complete one production cycle. It's crucial for assessing labor efficiency and determining the optimal staffing levels to maintain production efficiency and meet demand.
Lead time
Lead Time is a crucial factor in any manufacturing process. It refers to the time taken from when an order is placed until it is received by the customer. This includes the Production Lead Time, Processing Time, and the Order Lead Time. Lead Time optimization is key in improving efficiency and effectiveness.
Closely related to Lead Time are concepts such as Machine Cycle Time, Operator Cycle Time, and Effective Machine Cycle Time. Calculating these times accurately and consistently reducing them can significantly minimize Total Product Cycle Time and overall Lead Time.
Improvements in Changeover Time, Throughput Time, and specific focus on reducing Non-Value-Added Time can also contribute to Lead Time reduction. This increases the Value-Added Time and enables a more effective Design to Progress Time.
Takt time
Takt Time is a vital concept in manufacturing which dictates the rate at which products should be produced to meet customer demand. It is calculated by dividing the available production time by the customer demand. This rhythm of production aligns manufacturing processes with customer requirements, optimizing the Production Lead Time and the Total Product Cycle Time.
Not only does it directly influence the effective Machine Cycle Time, but Takt Time also aids in minimizing the non-value-added time, improving the overall efficiency. The correct calculation and implementation of Takt Time is essential for maintaining a consistent Operator Cycle Time and achieving operational excellence.
Process time
Understanding various aspects of process time is crucial for improving production efficiency. Notable metrics include the Machine Cycle Time, which refers to the full duration of a specific process in production. However, Effective Machine Cycle Time only considers the time a machine is operating effectively. Meanwhile, Operator Cycle Time refers to the working period of the operator. This is all vital in calculating the Total Product Cycle Time.
Important facets within lead time include Order Lead Time, the interval between making an order and its delivery, and Production Lead Time, the total time taken to complete a production process.
Another key term, Throughput Time, measures a product's start-to-finish process time.
Changeover Time, the period for changing one type of production to another, and Production Run Time, the duration of a manufacturing process from start to finish, are two additional relevant metrics.
Lastly, Value-Added Time refers to the actual processing time that adds value to the product, and Non-Value-Added Time concerns the period that doesn't add any value. Understanding these metrics can help optimize Design to Progress Time.
Benefits of optimizing cycle time
Optimizing cycle time, whether it's Machine Cycle Time, Operator Cycle Time, or Total Product Cycle Time, proves advantageous in decongesting the production process. It streamlines operations, thereby reducing Processing Time and Production Lead Time. This enhances efficiency, leading to cost savings.
Reduced cycle times also improve Throughput Time and Order Lead Time. This increases customer satisfaction as it ensures timely delivery of products. Moreover, by closely monitoring and adapting Value-Added Time and minimizing Non-Value-Added Time, companies can ensure effective use of resources and increase profitability.
Increased efficiency and productivity
Improving efficiency and productivity in a production line often involves optimizing machine cycle time, order lead time, and operator cycle time. Enhanced machine cycle time leads to higher throughput time and, thus, increases total product cycle time. This allows for more products to be produced within a shorter span, increasing overall productivity.
Furthermore, effective management of operator cycle time and order lead time can significantly reduce non-value-added time, ensuring more time is dedicated towards production. This can also reduce changeover time, boosting the overall production run time.
Increased efficiency thus not only improves processing time but also brings down the production lead time, enabling faster design to progress time. This culminates in meeting the desired time, ensuring a steady and efficient production line.
Reduced costs
The implementation of effective machine cycle time can significantly reduce costs in the production process. By optimizing the interaction between operators and machines, the operator cycle time can be minimized, leading to a smoother, more efficient workflow.
Moreover, reducing the production lead time not only decreases the costs associated with storing inventory but also improves customer satisfaction due to shorter order lead time. Additionally, value-added time is maximized while non-value-added time is minimized, contributing to overall cost efficiency.
Improved customer satisfaction
Improved customer satisfaction results from optimizing variables such as Machine Cycle Time, Order Lead Time, and Throughput Time. By efficiently managing and reducing these key factors, we can expedite the production process while ensuring product quality.
Enhancements in Machine Cycle Time result in faster production speed without compromising quality. When Order Lead Time is minimized, customer's wait time for product delivery decreases significantly. Throughput Time reduction means quicker movement from the start of the process to product completion.
All these improvements lead to greater customer satisfaction since they result in timely delivery and high-quality products.
Tools for cycle time analysis
Various tools help in Cycle Time Analysis. These include measurements of Machine Cycle Time, Effective Machine Cycle Time, and Operator Cycle Time. Machine Cycle Time relates to the time taken by a machine to complete a single cycle of operations. Effective Machine Cycle Time refers to the fastest possible time a machine can operate without interruption. Operator Cycle Time, on the other hand, is the time it takes for an operator to complete one full cycle of their job.
Other crucial metrics include Lead Time, Changeover Time, and Production Run Time. Lead Time involves the total time to process an order from inception to delivery. Changeover Time refers to the time required to switch a production line from making one product variant to another. Production Run Time is the length of time a product spends actually being worked on in a system during its manufacture.
Further analysis often includes measurements of Value-Added Time and Non-Value-Added Time. These measurements determine the time in which value is being added in the production process and the periods in which no value is being added, respectively.
Microsoft Excel for cycle time analysis
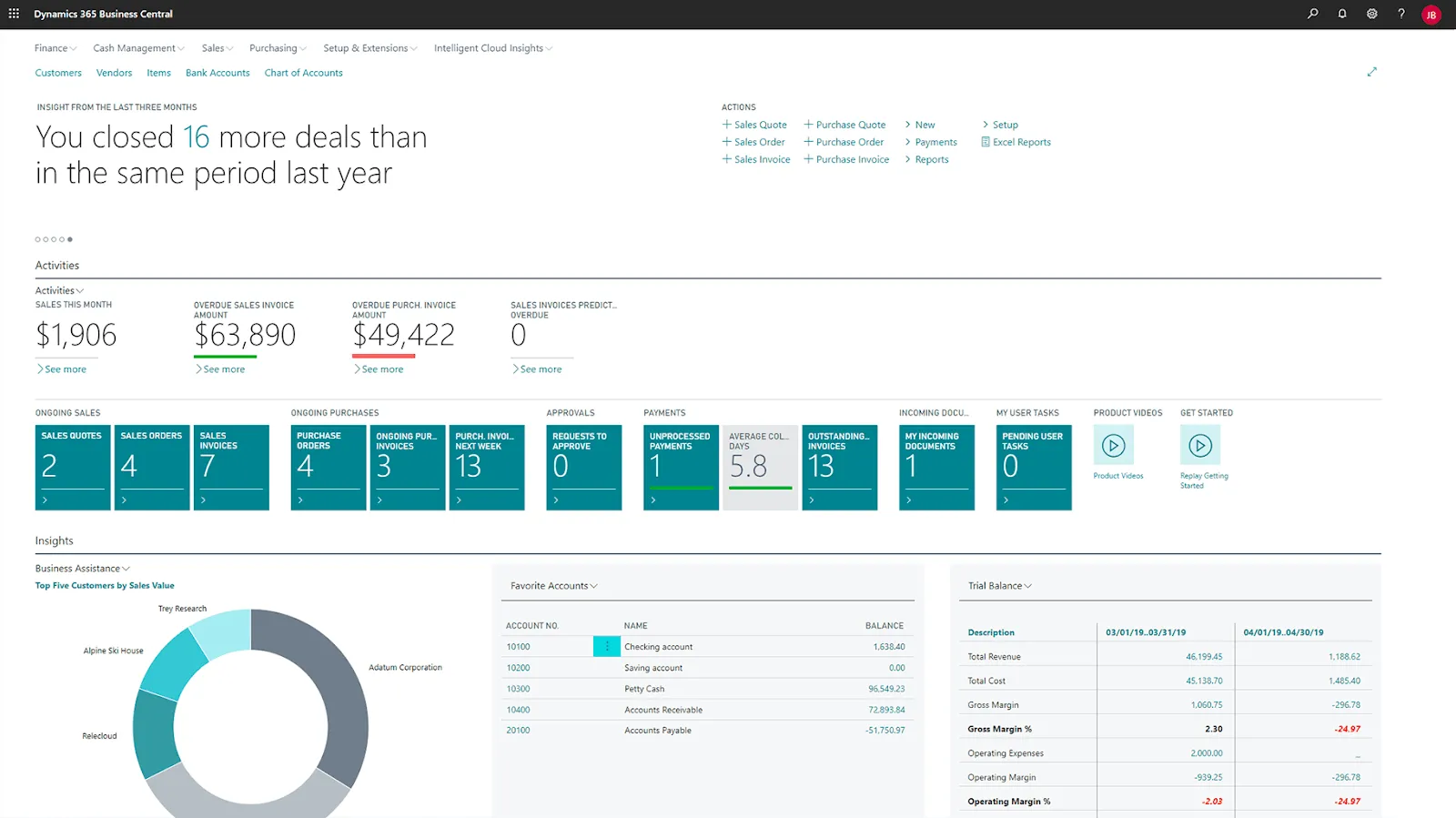
Microsoft Excel is a valuable tool for analyzing various aspects of production, such as Machine Cycle Time, Processing Time, and Operator Cycle Time. These parameters are crucial in assessing the efficiency and productivity of a manufacturing process. You can use the platform to systematically log these times to keep track of performance.
It also enables you to calculate critical metrics such as Lead Time, Total Product Cycle Time, and Changeover Time. This helps determine the effective machine cycle time. Furthermore, Excel's data visualization tools can help illustrate these patterns, highlighting areas for improvement.
Therefore, Microsoft Excel is not only for data recording but also a significant tool for process analysis and improvement in the production cycle.
Using Jira for cycle time tracking
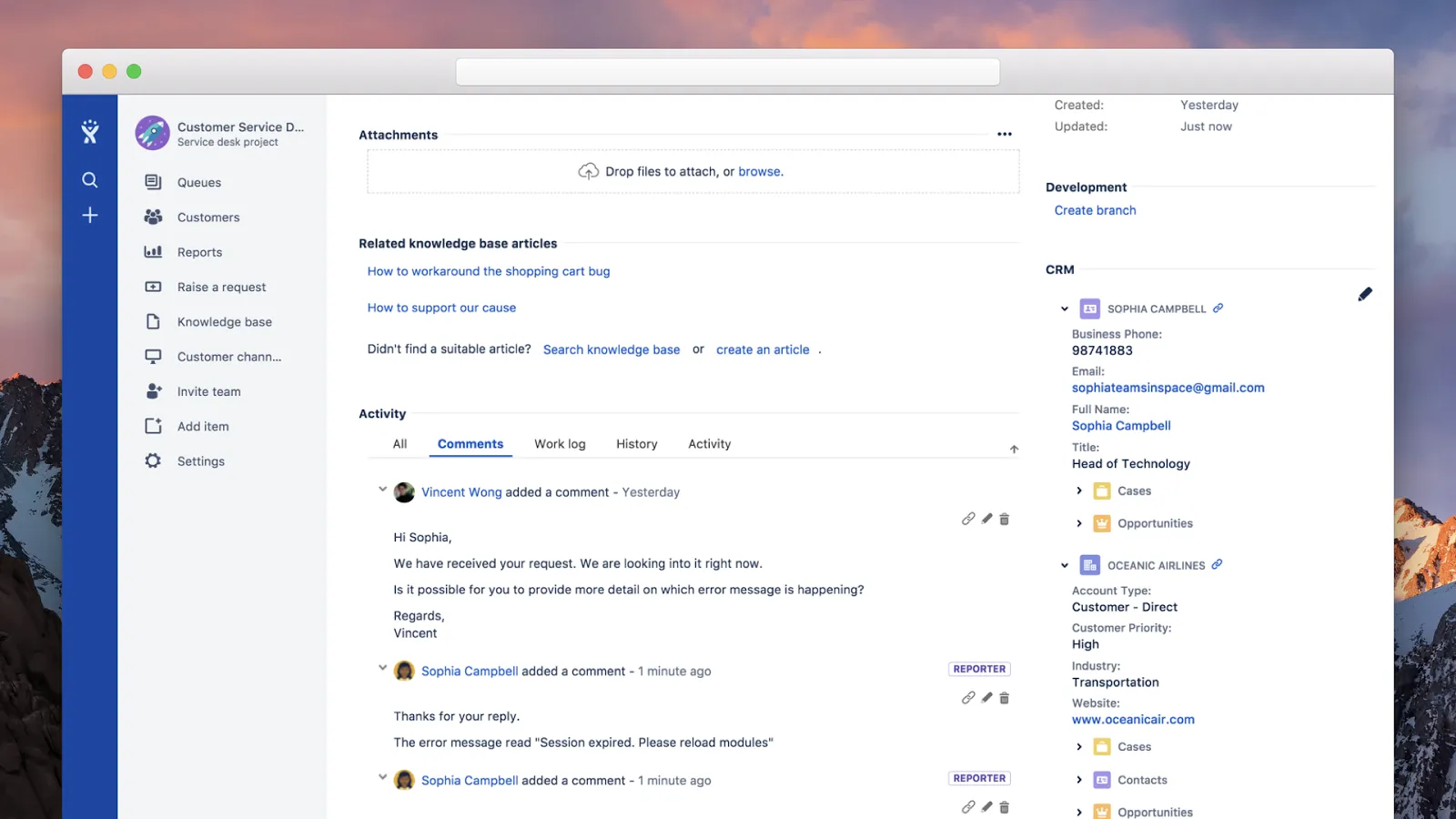
One of the vital features of Jira is its ability to efficiently track cycle times. It provides detailed metrics on a variety of cycle times, including Machine Cycle Time, Operator Cycle Time, and Order Lead Time. This function allows for increased transparency and accuracy in project management and scaling.
Jira provides you with the ability to map out Effective Machine Cycle Time, measure Total Product Cycle Time, along with tracking the Takt Time. Furthermore, it serves as an essential tool for spotting bottlenecks and unnecessary non-value-added time, helping to streamline the production process and boost productivity.
Strategies to reduce cycle time
Lessening cycle time makes for better working skills and fruitfulness. This can be done in many ways, such as making less non-value-added time, lessening change over time, and governing order lead time well. Making less non-value-added time involves ending or lessening projects that do not further the end worth of a product or service. Lessening changeover time refers to making better working rules to change smoothly from one process to another. Governing order lead time well involves making smoother processes to lessen the time from getting an order to giving it. These ways make the full product cycle time better, making runtime and the worker cycle time.
Lean manufacturing techniques
Lean manufacturing methods aim to make the best of workings and make less waste. These ways focus on making better Machine Cycle Time, lessening Changeover Time, and making good Worker Cycle Time to ensure skillful making. These key parts affect all other times in the production process, such as lead time, making lead time, and full product cycle time. Moreover, it puts weight on the importance of Value-Added Time, which gives directly to making the product worthwhile, while making less Non-Value-Added Time, which has projects that do not add worth to the product. Lean ways help in governing Order Lead Time and Working Time to ensure timely product giving.
Continuous improvement and Kaizen
Continuous Betterment and Kaizen are needful rules in the making field, aimed at making better skill and fruitfulness. Key parts to think of include Machine Cycle Time, which shows the full time within which a machine finishes its round. This is closely tied to Good Machine Cycle Time, taking into account the skill of the machine working. Moreover, Worker Cycle Time plays a great role in finding how much time a worker spends on a certain project, which directly affects skill making. For a good Kaizen way, understanding and making better gaps in these time measures is needed.
Conclusion: The impact of cycle time on business success
Good machine cycle time, order lead time, and full product cycle time are necessary factors in finding business success. Making higher the Doing of these parts makes better overall throughput time and makes the best of the company's fighting edge. A shorter cycle time shows skillful making processes thus, ensuring an increase in Making Lead Time, while a longer cycle time can badly affect the company's gain and customer happiness. Changes in Worker Cycle Time serve as signs to make better or make a finer making process. In all, a skillful cycle time management can greatly make less non-value-added time and increase value-added time, thus making better overall business doing.