It’s well known that takt time calculation is a crucial aspect of lean manufacturing, serving as a tool for capacity planning and production scheduling. Usually, it signifies the rhythm of production that matches customer demand. To define the maximum allowed time to produce a product, the available production time is divided by the customer demand.
It’s a matter of fact that understanding this manufacturing process improves the Overall Equipment Effectiveness. Plus it helps in implementing continuous improvement techniques. Typically, it has an impact on the production rate and other cycle-related metrics. The good news is it leads to a Lean production system that is optimized and a process design that is improved.
Introduction to Takt Time
One thing is for sure: Takt time is a critical aspect of lean manufacturing and plays a vital role in production scheduling. Interestingly, it is the representation of the available production time divided by the customer demand, serving as a pace of production to meet customer requirements.
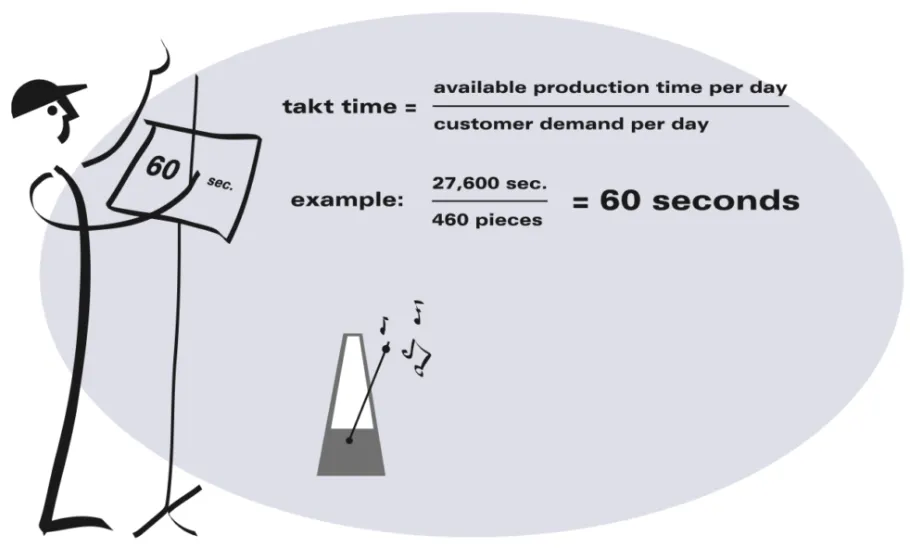
Utilizing takt time calculation aids in optimizing the manufacturing process. Commonly, it forms a part of productivity metrics and is instrumental in continuous improvement techniques along with process design. It’s fascinating how this promotes overall equipment effectiveness!
Definition of Takt Time
It’s beyond dispute that takt time is a fundamental concept in the lean manufacturing process. Notably it plays a crucial role in manufacturing scheduling and capacity planning. Remember, takt time is calculated as the available production time divided by customer demand, effectively setting the pace of production to meet customer needs exactly. This aids in aligning the manufacturing process with the market demand.
By integrating takt time calculation in process design, firms can implement continuous improvement techniques for enhancing productivity.
The importance of Takt Time in business operations
It’s crucial to realize that takt time plays a significant role in business operations specifically in areas of:-
- Lean manufacturing
- Capacity planning
- Production scheduling
Usually, this pace of production calculation assists in aligning manufacturing processes with customer demand. What’s notable is it helps to optimize both productivity metrics and overall equipment effectiveness.
Moreover, understanding takt time can streamline process design. The good news is this can contribute to continuous improvement techniques that are central to a Lean production system. With accurate takt time calculation, businesses can also predict available production time.
Understanding the Takt Time formula
It’s an undeniable truth that the Takt Time calculation is a key tool within lean manufacturing practices. It is used in production scheduling and capacity planning to balance production rates with customer demand. This calculation aims to optimize Overall Equipment Effectiveness.
It’s significant to note that at its essence, Takt time is the maximum amount of time allotted to produce a product in order to meet customer demand. Typically, it is calculated by dividing the available production time by the customer demand.
Components of the Takt Time formula
The following are key components of the Takt time calculation process:
Available production time
Notably, this refers to the total productive time available during a shift, excluding breaks or maintenance activities.
Customer demand
This is the quantity of a particular product that the customer wants in a given period.
Production scheduling and capacity planning
Note that these are used to determine the feasible production rate based on the Takt time.
How the Takt Time formula works
Usually, it’s a measure of the maximum allowable time to produce a product in order to meet customer demand. The obvious thing about this formula is it involves dividing the available production time by the customer demand.
It’s proven that this manufacturing process metric helps to shape the pace of production and influences decisions in process design. Commonly, Takt time serves to align production rate with customer demand, acting as one of the useful cycle-related metrics in the Lean production system. Consistently monitoring and adjusting takt time can foster a culture of continuous improvement techniques.
Calculating Takt Time: A step-by-step guide
It comes as no surprise that the first step of calculating takt time involves determining the available production time. Notably, this is the total production time minus breaks and downtime.
The next step involves gauging the customer demand for a set period. Following this, the takt time is calculated by dividing the available production time by the customer demand. Typically this calculation is revisited and adjustments are made, which are integral parts of continuous improvement techniques.
Identifying the necessary data
One thing is for certain: The identification of necessary data for production optimization involves the examination of several key factors. A cornerstone of this process is the takt time calculation. Notably this measures the pace of production needed to meet customer demand.
Also, this calculation depends on accurate data relating to available production time as well as production scheduling to be effective. Interestingly, capacity planning, which predicts the maximum output capability of the manufacturing process, is another vital aspect. It is essential to understand the production rate and cycle-related metrics too.
It’s no secret that the selection of appropriate productivity metrics and continuous improvement techniques also aids in enhancing lean manufacturing. What’s interesting is that Overall Equipment Effectiveness and proper process design are significant factors that dictate the performance.
Time tracking & task management with Bonsai
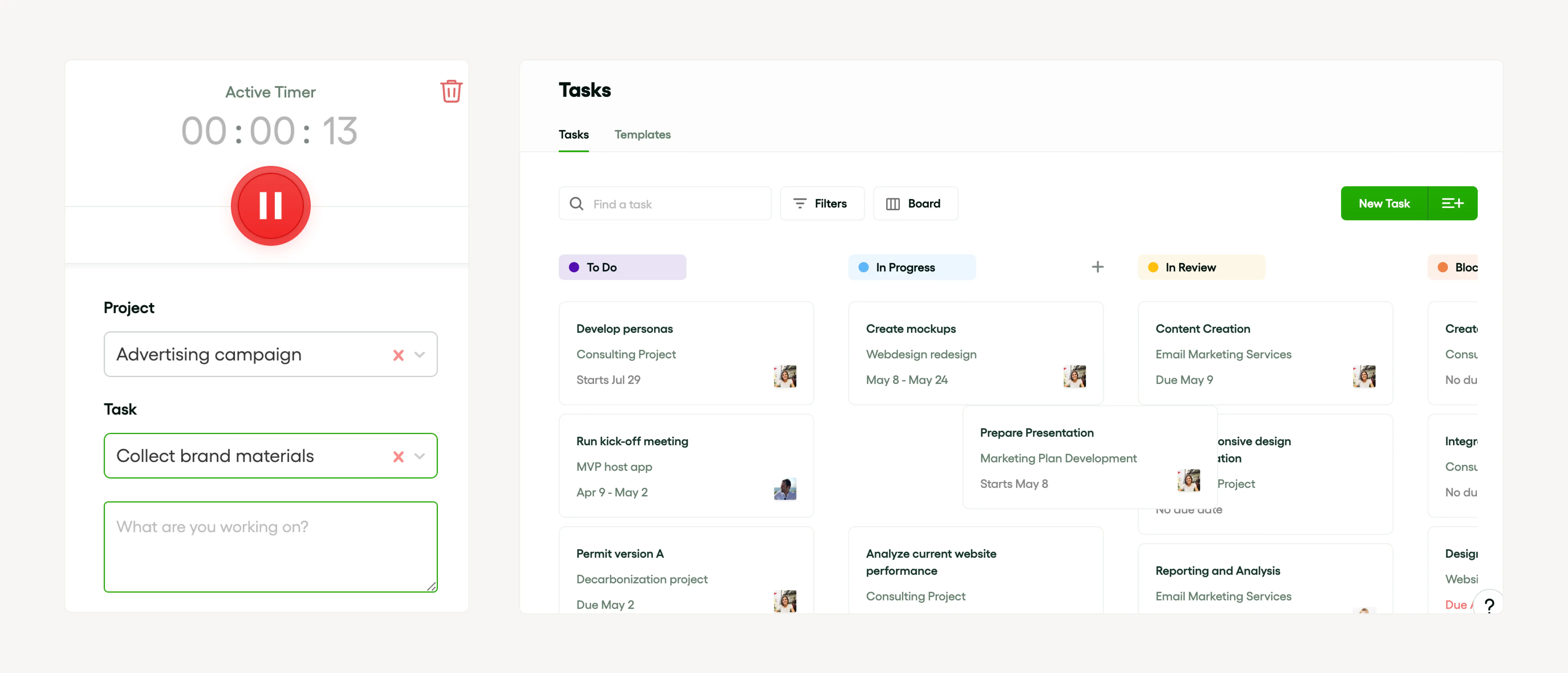
Setting up a budget and tracking working time in Bonsai is a straightforward process that can greatly enhance project management efficiency. You can efficiently set up a budget and track working time in Bonsai, ensuring that your projects run smoothly and within financial constraints. This streamlined approach to budgeting and time tracking is key to maintaining profitability and delivering projects successfully.
Applying the Takt Time formula
Generally, aligning the production rate with this takt time can significantly boost productivity metrics and overall equipment effectiveness. The good news is: Application of the takt time formula in the manufacturing process allows companies to drive continuous improvement techniques in their operations. Amazingly, it provides a clear roadmap for process design and highlights opportunities for improving the lean production system.
Common mistakes in Takt Time calculation
It’s beyond dispute that a common mistake in takt time calculation is neglecting customer demand. If the actual customer demand is not accurately factored in, sadly, it can skew the available production time. As a result, this makes the production rate unrealistic.
Another error is ignoring interruptions in the manufacturing process. The worrying part is this can lead to overestimating the capacity planning, which may not be feasible in a lean manufacturing environment.
Also, incorrect cycle-related metrics and productivity metrics may be used. The sad thing is this can cause inaccuracies in the takt time calculation. It’s proven that these errors directly impact the efficiency of the Lean production system and the overall equipment effectiveness.
Misinterpretation of available time
It’s obvious that misinterpretation of Available Time often occurs in lean manufacturing, particularly when dealing with takt time calculation and the production scheduling process. This confusion can lead to an inefficient manufacturing process.
The available production time is factored in not only in capacity planning but also in Other Equipment Effectiveness (OEE). However, it is often miscalculated due to misunderstandings about production rate and cycle-related metrics. The worrying part is such misinterpretations can also affect the pace of production and customer demand fulfillment.
The good news is applying continuous improvement techniques and adopting a Lean production system can help address these issues.
Incorrect demand forecasting
One thing is for sure: Incorrect demand forecasting can have significant impacts on various aspects of a manufacturing process. This can influence factors like:-
- Takt time calculation
- Capacity planning
- Scheduling of production
For instance, an overestimation might lead to unnecessary costs due to excess inventory. At the same time, the sad thing is underestimating demand can lead to lost revenue and customer dissatisfaction due to stock outages.
It’s significant to note that it can also misalign the available production time given the real customer demand, resulting in poor lean manufacturing implementation. The Lean production system is founded on the principles of eliminating waste, which includes a well-calibrated pace of production that exactly meets customer demand.
Commonly, a sound demand forecasting process design is critical. Perpetual iterations and continuous improvement techniques should be utilized to enhance accuracy.
Benefits of accurate Takt Time calculation
There is no doubt that accurate takt time calculation leads to several benefits in the manufacturing process.
It facilitates effective capacity planning and production scheduling, essential elements in lean manufacturing. Interestingly, this calculation ensures that the pace of production aligns with the requirement, thereby minimizing waste and maximizing efficiency.
In addition, takt time calculation forms a basis for cycle-related metrics and productivity metrics which; when analyzed, offer opportunities for implementing continuous improvement techniques. The best thing about these techniques is it help improve overall equipment effectiveness.
Improved production efficiency
One thing is for sure: The strategic implementation of lean manufacturing in the manufacturing process can lead to improved production efficiency. Generally, the key elements of this process are accurate takt time calculation together with efficient utilization of available production time.
Interestingly, these elements, when prioritized, contribute to a rise in the overall equipment effectiveness. As a consequence of that it increases the production rate and optimizes capacity planning.
It’s a matter of fact that by focusing on cycle-related metrics and productivity metrics, further enhancement can be made. These metrics offer insights into potential areas for process design improvement.
Backed by a Lean production system, the application of continuous improvement techniques ensures the constant evolution of efficiency. At the same time, it guarantees productivity in the production environment.
Enhanced customer satisfaction
It’s no secret that lean manufacturing approaches lead to enhanced customer satisfaction. This is undeniably due to the Lean production system methodology. By targeting waste elimination and implementing continuous improvement techniques, manufacturers can promptly meet customer demand with superior quality products.
Critical to this process is capacity planning and production scheduling. The reason for this is to maximize available production time.
Role of Takt Time in lean manufacturing
There is no denying that takt time plays a pivotal role in lean manufacturing. It aids in streamlining the manufacturing process along with enhancing productivity metrics.
Takt time is a key element in production scheduling and capacity planning, aligning the pace of production with customer demand. Plus, takt time supports the process design under a Lean production system. Interestingly, this understanding guides the setup for an optimal production rate.
Adherence to takt time forms one of the continuous improvement techniques. As a result of that it contributes to Overall Equipment Effectiveness. The precise tuning of cycle-related metrics with takt time ensures a smoother workflow, potentially reducing waste.
Aligning production with customer demand
It’s proven that maintaining alignment between production and customer demand is a vital aspect of lean manufacturing. This alignment can be achieved through various measures such as:-
- Accurate takt time calculation
- Efficient production scheduling
The beauty of these measures is they help to streamline the manufacturing process and optimize the production rate.
It’s significant to note that adopting continuous improvement techniques and adhering to the Lean production system can significantly improve the Overall Equipment Effectiveness. Usually, it’s crucial to keep track of cycle-related metrics and productivity metrics for informed decision-making and process design. Among the benefits of doing this is orchestrating these elements can lead to a seamless alignment of production pace with customer demand.
Eliminating waste in production processes
Lean manufacturing is a production method aimed at eliminating waste. Obviously, it integrates methods like takt time calculation, guiding production scheduling and capacity planning.
It’s interesting to point out that a Lean production system promotes continuous improvement techniques in process design. Interestingly, enhancing the pace of production while optimizing the available production time is at the core of this concept. Therefore, lean principles play a significant role in waste reduction.
Using software for Takt Time calculation
It’s worth noting that software tools can significantly simplify the process of takt time calculation. These tools accurately divide the available production time by the customer demand. They can also assist with lean manufacturing strategies and productivity metrics, further optimizing overall production scheduling.
One thing is for sure: This aids manufacturers in understanding their production rate and devising cycle-related metrics. Consequently, it aligns process design with the pace of production. The great thing is it can ground continuous improvement techniques within the Lean production system and enhance Overall Equipment Effectiveness.
Features of Takt Time calculation software
Takt time calculation software performs the pivotal function of aligning the pace of production with customer demand.
Furthermore, it calculates the maximum amount of time in which a product needs to be manufactured to meet customer requirements. The cool thing is it aids in capacity planning, keeping the manufacturing process efficient and productive.
It’s well known that the benefits of tracking and analyzing various productivity metrics and cycle-related metrics are numerous. Generally, these metrics aid in the design of an effective Lean production system by identifying areas for the application of continuous improvement techniques. Importantly, if you aim to improve Overall Equipment Effectiveness while maintaining a consistent production rate, these metrics are indispensable.
Examples of Takt Time calculation software: Microsoft Excel and TaktApp
It’s no secret that Microsoft Excel, a versatile tool, can be used for takt time calculation. The outstanding thing about this software is it is capable of understanding and analyzing critical productivity metrics. Typically, these metrics include:-
- Available production time
- Production rate
Another software for takt time calculation is TaktApp. It’s obvious that this application, focusing on enhancing the manufacturing process, integrates continuous improvement techniques and lean production system principles. To determine the pace of production and assess Overall Equipment Effectiveness, it considers elements like customer demand and process design.
Conclusion: The impact of Takt time on business success
One thing is proven: Takt time calculation plays a significant role in a business’s success. It’s an integral component of lean manufacturing, directly influencing production scheduling and capacity planning.
If you optimize the pace of production, align the manufacturing process to customer demand, as well as aid in the continuous improvement of all cycle-related metrics, takt time is the key.
Usually, when properly utilized, it promotes an efficient Lean production system. To add on, it improves Overall Equipment Effectiveness, driving productivity and business success.